More than 27 million kitchen appliances manufactured by Peterborough-headquartered white goods maker Whirlpool are located in homes across the UK.
And the task of liaising with customers, diagnosing faults with tumble driers, washing machines or fridges, carrying out repairs either via a mobile phone or by an engineer in person, delivering ordered products or retrieving old ones falls in large part to the 1,000 dedicated staff at Whirlpool’s premises in Morley Way, Woodston.
It is the location for 350 call centre staff, a reprocessing and recycling centre, plus an engineers training academy and its factory outlet where repaired machines are sold to staff and the public at heavily discounted prices.
And with so many of its products installed in people’s homes it is no surprise that Whirlpool gives customer service its highest priority.
And it is a vision of customer service that also seeks to minimise the company’s impact on the wider environment under the motto of ‘Home includes the planet’.
It starts with the call centre where staff are the first point of contact with the company. Contact can be made through the telephone or via social media around the clock. Contact through social media is currently double that of last year. But a customer need not wait for an engineer to call at their home.
Staff at the centre can even connect through a customer’s mobile phone and using the camera app can get a view of the machine and identify its fault and often help correct it.
This means the number of trips the firm’s engineers have to make is kept to a minimum.
All machines can be kept running for as long as possible with the help of the factory's parts centre which contains 6.6 million individual parts for a range of machines that sometimes can be 10 or 15 years old.
Whirlpool also has a centre dedicated to checking out returned machines and parts and which when repaired and tested then go into a ‘factory shop’ and sold at discounted prices to staff and the public.
All of Whirlpool’s engineers are trained in Peterborough and get to work on the full range of Whirlpool machines from over the decades.
The company is investing in electric powered vans as it looks to reduce its impact on the environment.
Its home delivery team have trained more than 1,000 drivers, mates and supervisors since 2014 and each year a delivery driver will drive more than 40,000 miles and deliver more than 5,000 appliances.
Stephen Hodgson, customer services operations director, said: “We produce innovative machines, particularly Hotpoint, which goes back 100 years in the UK.
“Everyone here is passionate about supporting the brands and passionate about our consumers.
He said: "We have a 360 degree model from designing the product, selling the product and now what has become really important, keeping the product in the customers’ homes.
"As customers have invested in a product, when it goes wrong they want to phone someone who will have empathy and solve the problem quickly and keep that product in their home.”
Marco Bellinzona, senior consumer service director, said: “We are proud that we are approachable. Customers can call us at any time.”
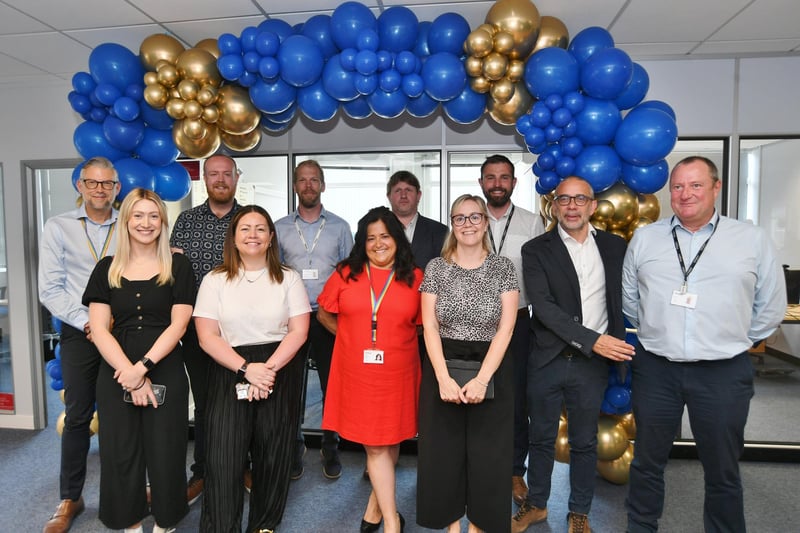
1. Whirlpool at Woodston
Some of the call centre team at the Whirlpool factory in Woodston, Peterborough. Photo: David Lowndes
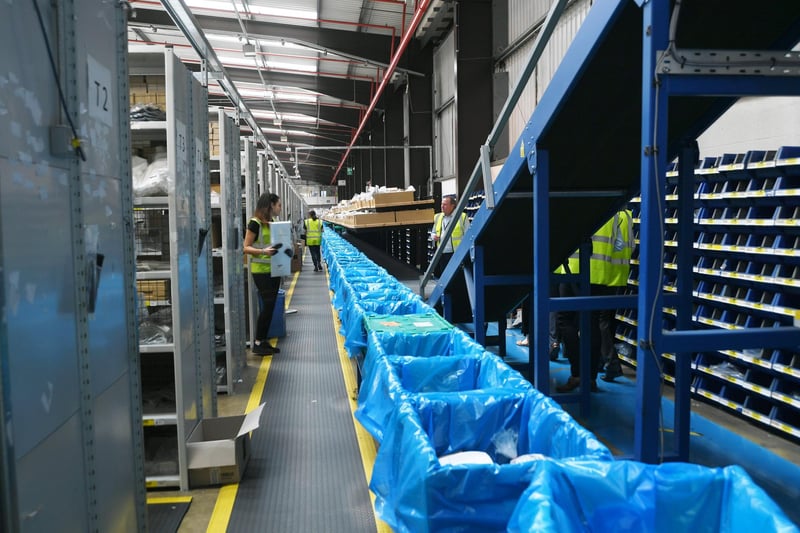
2. Whirlpool at Woodston
A conveyor belt takes the parts around the factory at Whirlpool in Peterborough. Photo: David Lowndes
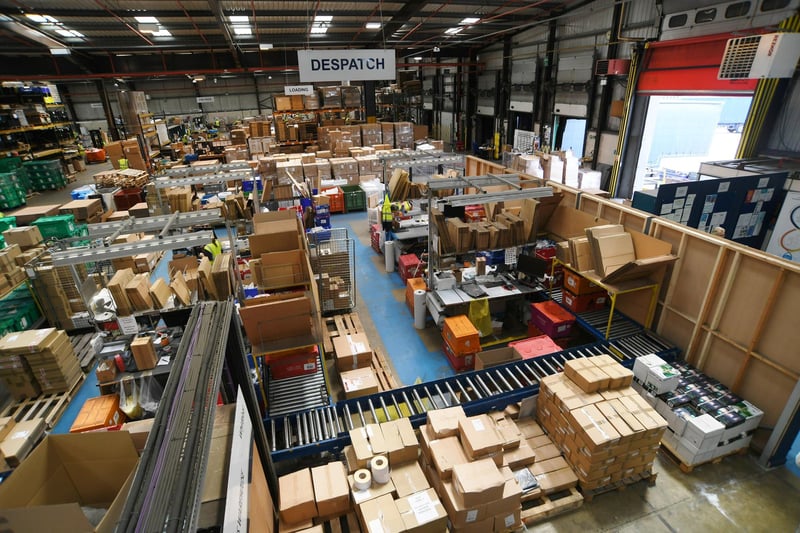
3. Whirlpool at Woodston
The parts warehouse at Whirlpool in Peterborough. Photo: David Lowndes
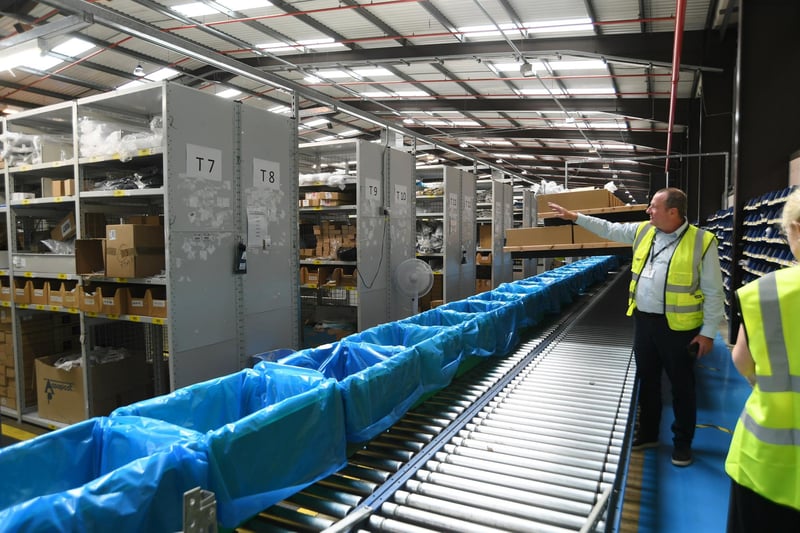
4. Whirlpool at Woodston
A conveyor belt takes the parts around the factory at Whirlpool in Peterborough. Photo: David Lowndes