The future techniques of mass manufacturing are being shaped in the new headquarters of a Peterborough company.
3D printing specialist Photocentric has moved into new offices, labs and warehouse at Titan House, in Titan Drive, Fengate, in a relocation that has cost, so far, in excess of £7 million.
The 5,500 square metre centre of excellence features 1,275 square metres for three state-of-the-art print farms for industrial parts, dental aligners and ceramics plus 1,400 square metres for 3D hardware production facility as well as a 25-desk sales and service office.
At its centre is a new machine named Jeni – named after the Spinning Jenny of the Industrial Revolution that helped pave the way for mass manufacturing to take place in what had been a cottage industry.
It is this disruptive impact that Paul Holt, founder of the triple Queen’s Award winning Photocentric, hopes the autonomous Jeni – the first of its type – will have on current manufacturing, using 3D printing to allow vast quantities of materials to be produced – digitally, cheaply, sustainably and with little labour.
And through a Government Innovate grant of £2.5 million, Photocentric is working with leading companies Unipart, Games Workshop and Essentra Components to help transform their manufacturing processes.
At the heart of the process is Liquid Crystal Display technology powering arrays of 3D printers. This automated digital process uses single-flow production lines that start with liquid resin and autonomously deliver useable plastic objects at the other, in scale.
Mr Holt said: “What we are doing here is unique.
"The question we’ve been trying to answer is why is 3D printing not making every day items? Unless people use dental liners or hearing aids, they will never touch a 3D printed product.
"The clue as to how to do it came out of a contract we had to make PPE at the height of the Covid-19 crisis.
"We found a way to mass manufacture the face shields for health workers and made two million of them.
“Now we’re constructing a mechanism to make millions of products of all types."
He hopes Photocentric’s work can help Peterborough evolve from a warehouse picking, packing culture to a highly paid, high tech manufacturing city.
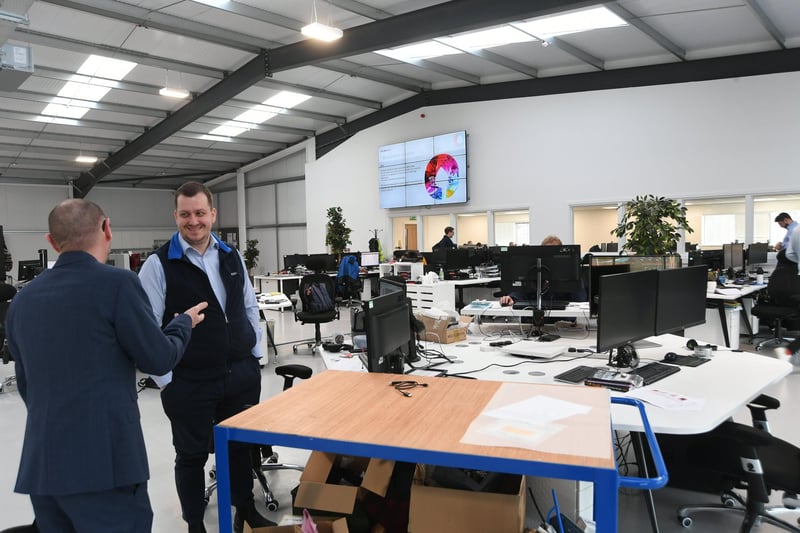
1. The future of manufacturing at Photocentric
Inside Photocentric's new premises at Titan Drive, Fengate, Peterborough. Photo: David Lowndes
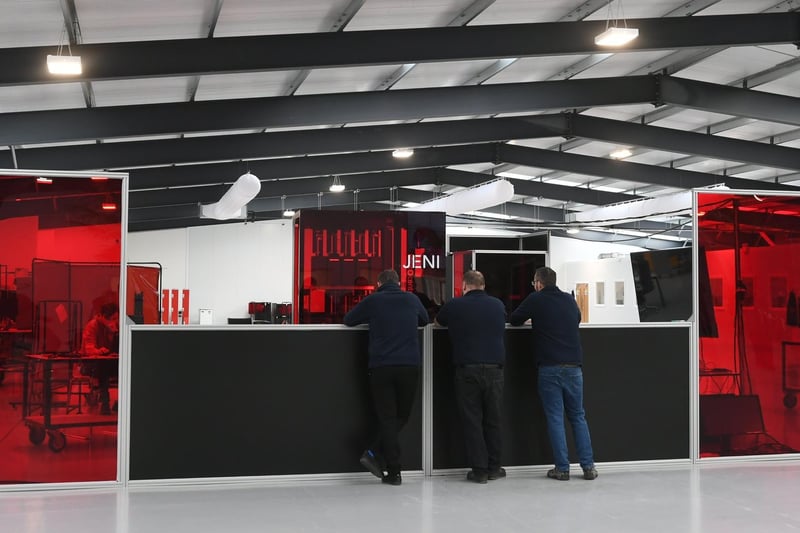
2. The future of manufacturing at Photocentric
Staff monitor Photocentric's new Jeni 3D Printing system. Photo: David Lowndes
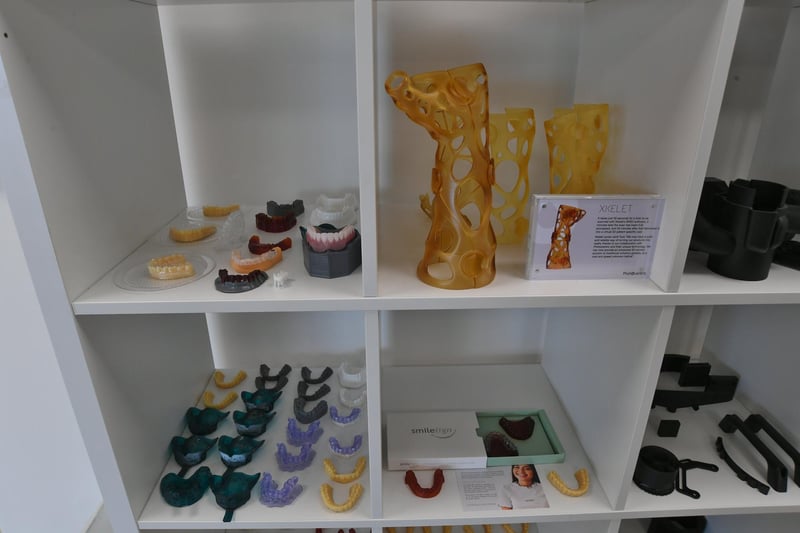
3. The future of manufacturing at Photocentric.
Some of the products manufactured by 3D printing at Photocentric at its new premises in Titan Drive, Fengate. Photo: David Lowndes
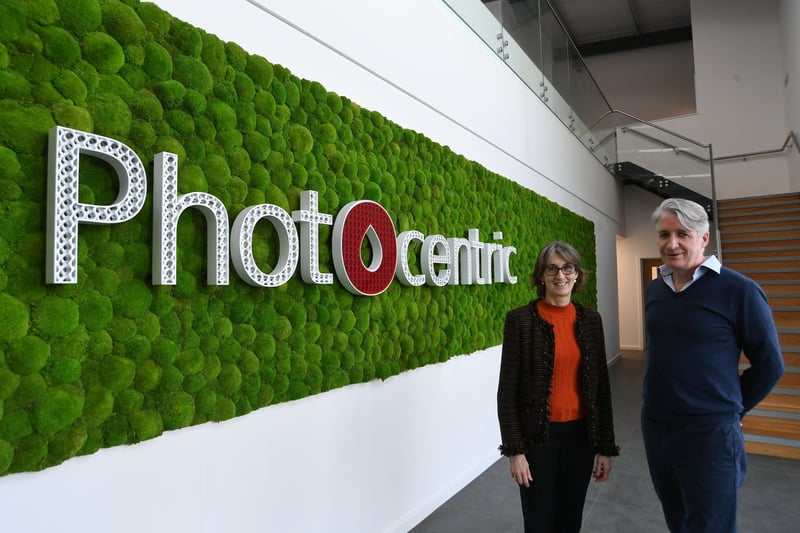
4. The future of manufacturing at Photocentric.
Photocentric founder Paul Holt with Cristina Sesma, Group Marketing Manager Photo: David Lowndes